The technology that may transform trash into treasure
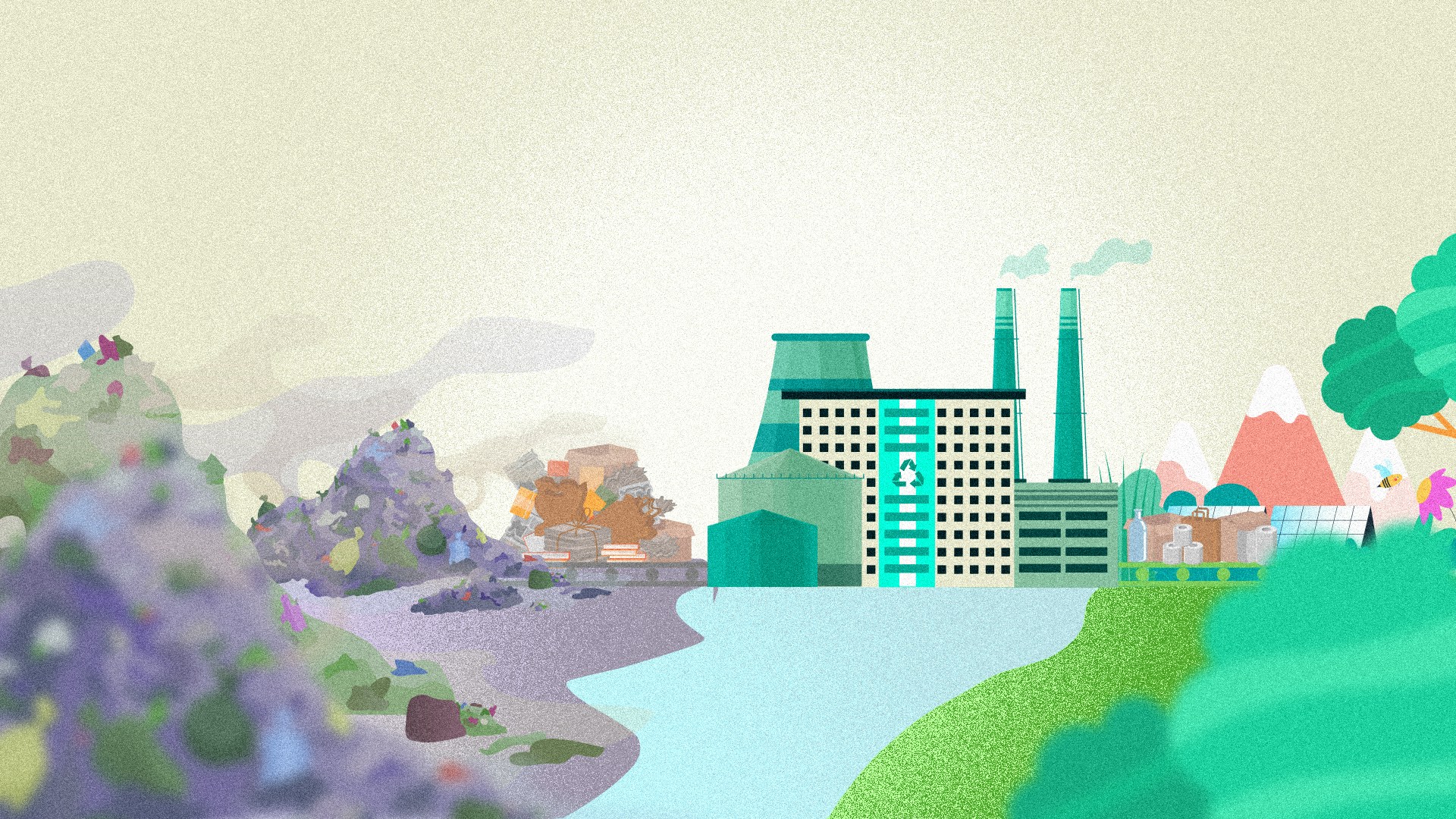
As I stand on a gantry overlooking the cavernous hall of the SUEZ Recycling and Recovery Plant outside Bristol, in the UK, I’m struck by how calm it is. Before my visit, I envisaged a never-ending tsunami of waste piling onto thunderous machines straining under the weight of garbage. Instead it is an orderly flow of ascending refuse, separating at each stage and resulting in neat, compressed waste cubes stacked across the far wall.
It left me feeling that maybe technology—and a healthy dose of behavioural change—could provide a means to fight back against our devastating waste problem while turning a good chunk of garbage back into something useful.
The trash we make
We may be approaching several solutions that could help turn the trash tide away from landfill, but we can’t sugarcoat our consumption and disposal habits. We throw away too much and recycle nowhere near enough, generating massive environmental impacts. Those who live in the west produce a literal metric tonne of waste every year.
The average EU household (containing 2,3 persons) throws away nearly 1,2 tonnes of waste per annum, or 513 kg per person.
That number is higher in the US, with the last available figures (for 2018) showing the average American puts over 2 kg of trash in the bin every day, generating an average of 811 kg per year. This is the fruit of an incredibly dramatic change, with the amount of municipal waste generated in the US rising 93 percent between 1980 and 2018.
Concerningly, progress on recycling has been, at best, uneven in many western countries. Though total household waste produced in the UK has remained steady over a decade, declining slightly between 2022 and 2015, the recyclable percentage of this waste has gone nowhere, decreasing marginally from 44,5 percent in 2015 to 44,1 percent in 2022.
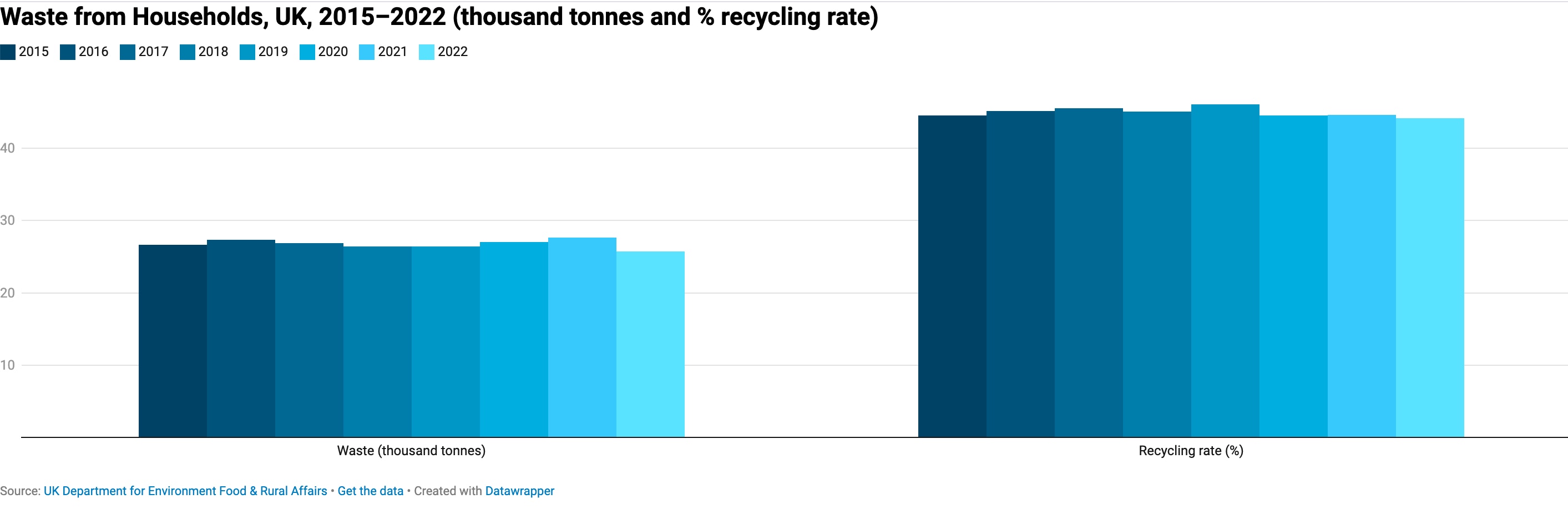
This existential issue was exacerbated in 2017-2018, when the world’s largest importer of refuse—China—changed course. The government had enough of receiving Western rubbish and banned solid waste imports, leading to the biggest shakeup in waste material supply chains for decades. At a stroke, China’s imports of plastic were cut, dropping 95,4 percent within a year of the ban; as were imports of waste paper, inducing a scramble to find new solutions.
But what of less wealthy countries, where the average citizen consumes less and therefore produces less waste? Perversely, the problem is even more acute.
Issues around water and food cleanliness make plastic-packaged consumables highly attractive in these environments, but there is often limited infrastructure to collect, never mind process, municipal or commercial waste. This creates massive piles of refuse that often end up in waterways, yielding considerable contamination from urban areas to the middle of our oceans. For several Southeast Asian countries, China’s waste ban worsened the problem, as many previous waste exporters found themselves seeking somewhere new to dump rubbish.
This leaves us with a huge legacy of environmental degradation, the devastating impacts of which are becoming clear. Plastic bags have been discovered in the depths of the Mariana Trench, while microplastics have been found on the slopes of Everest. More recently, microplastics were found in every single human placenta and testicle investigated in two different studies.
Sorting a haystack of needles
The fundamental problem with trash is that there’s so much.
This isn’t merely a volume issue but one of variety. Plastics, fibres, glass and metals all go in bins, forming a bewildering range of packaging shapes and colours, along with a large quantity of related contaminants.
These are all “people’s needles in my haystack,” says my knowledgeable guide around the recovery plant, SUEZ’s Chief Technical Development and Innovation Officer, Stuart Hayward-Higham. “The more you mix it, the bigger the haystack,” he comments, providing multiple examples of how complex this task is.
If cardboard is too wet, or paper too thin or small, it is likely to exit the recycling process. If a plastic bottle contains too much liquid, the machinery may struggle to sort it correctly. If plastic is coloured, it can only be processed into a darker shade at the next stage. If an object is obscured under another, it might not be sorted properly.
One way to reduce this issue is to sort recycling before it arrives at a reclamation centre. However, there will always be mixed trash streams and the need to perform some level of sorting even when materials are broadly separated.
Additionally, the plants need to become more efficient. The large facility I visited squashes each garbage truck load delivered down to around one-fortieth of its original size and processes 65.000 to 75.000 tonnes per year, but even this is not enough. The UK alone would need hundreds of these to achieve a high recycling rate across household and commercial waste.
To drive up efficiency and escape the mess we’ve made, we must turn—at least in part—to technology.
Perceiving treasure in trash
The impact of technology can be felt in three main areas: identifying, sorting and reprocessing materials.
Essentially, you need to know precisely what the type of waste is, separate out the materials so they are homogenous, then be able to turn that into something useful.
It’s worth pausing briefly on that last part, because most of this rubbish has value as feedstock, a value that goes up the less reprocessing is required. That can change substantially, depending on market conditions.
For example, metals are infinitely recyclable and are the easiest material to sort via magnets. That makes something like aluminium worth around €1.400 to €1.700 per tonne, far cheaper than newly mined aluminium.
Values for reclaimed materials can then fall to a few tens of euros per tonne for the lowest-grade glass, with plastic and fibres sitting in between, depending on the exact material and its condition, but still holding notable resale value, especially when wider market supply of virgin materials is limited. The Russia-Ukraine war pushed prices for plastics up 39 percent year-on-year to €454 euro per tonne, underlining not just the monetary value, but the potential for greater supply chain security from more circular material usage.
Turning back to our three key problems, Hayward-Higham thinks that it is those first steps, identification and sortation, where the biggest leaps are happening.
One of the key machines SUEZ uses at the Avonmouth site is an elegant solution to the plastics problem: Shining infrared light at plastics and using the different reflected wavelengths to figure out what the material is. It then directs blasts of air to push them above the waste stream into a separate conveyor belt. This system of “ballistic separation” is repeated for clear and non-clear plastic, then for different plastic types, and is now common in the industry.
However, Hayward-Higham thinks this process can become better and more universal through computer vision and better labelling.
“The big [technology] will be the development and the skill that visual artificial intelligence (AI)” will introduce in identification, Hayward-Higham thinks.
As observed in a previous feature in this series, AI visual analysis has made massive gains over the last decade. It is almost tailor-made tech for refuse sortation.
While their current detectors “can do clear and non-clear, and they can do resin-by-resin,” Hayward-Higham explains. “It can't go, ‘Oh, that's a milk bottle and that's a detergent bottle’.”
But an AI system “can look at items the same way that you recognise them on the shelf as different,” down to “using the shape and look of a Coca-Cola bottle to separate it from a Pepsi bottle or a can,” he says, potentially even using the stylings of different packages as an advantage rather than the handicap they currently present.
What’s more, visual AI is at its best when it can learn from lots of repeatable data. The vast amount of waste means this isn’t in short supply.
This could be potentially combined with the emerging technology of digital watermarking. The watermark is an imprinted code invisible to the naked eye that would immediately, and accurately, identify the exact plastic resin that forms the packaging when scanned, like when phones read a QR code.
This remains at a trial stage, which limits the potential, as “it needs to be system adopted,” says Hayward-Higham. “It can't be that one or two producers adopt it, and others don't.”
At the recovery facility, systems incorporating visual AI are actively being used, including cameras that analyse the composition of material passing along conveyor belts and direct workers to pick out key materials with light. SUEZ claims these have increased the number of items correctly picked by half, and increased the value of recovered materials by 77 percent at this particular stage.
To see full potential though, these systems need to be deployed at a more ambitious scale, which also allows them to achieve much-needed efficiency gains.
Between Sweden’s two biggest cities is Site Zero. At this facility, plastic waste passes along a five-kilometre sorting line armed with lasers, cameras and near-infrared and electromagnetic sensors at more than 60 sorting stations. The refuse is pushed, shaken, sieved, rotated and scanned across this lengthy journey so it can fall into one of 12 different types of plastic.
The end result is that this single facility can take in around 200.000 tons of plastic waste, or all the plastic packaging Swedish households throw out annually, and still push out 95 percent recyclable material.
Eating and heating to remake materials
Critically, having cleaner streams of waste makes the next stage—turning materials back into something useful—vastly more productive.
Whether it is cardboard, glass or plastics, having streams of similar materials in terms of chemical composition and state of decomposition reduces the cost and steps required to remake them.
But fibres and plastics break down as they get reprocessed, limiting the number of times they can undergo processing. Many materials are extremely hard, or impossible to currently recycle. That will have to change if we are to have a shot at a circular economy where nearly all materials are reused.
For the most difficult man-made materials, nature could provide us with one of the best potential solutions.
Bioremediation, or removing pollutants with organisms, didn’t initially come from a lab, but from discovered examples of organisms happily chowing down on waste in various environments.
While some bacteria were known to consume man-made hydrocarbon products before 2016, this year was pivotal due to a paper from Japanese researchers that catalogued the first known PETase. This bacteria-made enzyme was found eating the PET (Polyethylene Terephthalate) plastic bottles from a nearby bottle recycling plant. The PETase enzyme breaks bottles down into hydroxyethyl terephthalic acid, then a second enzyme, MHETase—fully mapped out in 2019—goes to work on the acid. The end result is ethylene glycol and terephthalic acid. Those are the precursor chemicals for PET and so can be remade back into bottles.
Since then, researchers found multiple other examples of not just bacteria but fungi that can consume an amazingly broad range of materials, including highly toxic ones such as PFAS, the most well-known of a variety of “forever chemicals.”
Progress in genetic engineering, genetic sequencing, protein engineering and machine learning means finding related enzymes that work faster has become easier. Bacteria’s genetic material can be edited and tested quicker. Already, companies are using bacterially broken-down chemicals to make new PET bottles.
A similar concept, but a very different method, is pyrolysis, which uses chemicals and heat in an oxygen-free environment to break materials down into reusable chemicals. While this does require input energy, and the net carbon impact is disputed, simply incinerating waste was recently found to be more polluting than even coal, meaning the typically preferred alternative to recycling is not viable in the long-term.
Pyrolysis breaks down chemical bonds in hydrocarbon chains. In the case of plastics and tyres it results in gases, oils and carbon outputs (and a small amount of steel tyres).
The jury remains out on whether this is a feasible solution at scale to plastics. Handling mixed plastic with contaminants is tricky because it creates a chemical cocktail that separates at different temperatures, producing unintended bonds without complex and expensive management techniques. Uses of catalysts and breaking down plastics with superheated steam show potential in improving the process, creating outputs that need less additional processing and input energy, though they too are still being tested at industrial scale.
However, for tyres, plants are being built around the world and it represents the only real way of recovering a previously unrecyclable and extremely environmentally damaging product.
These models aren't perfect. The oils and gases often require further refining, and those remain fossil fuels, often destined to be burnt in diesel and ship engines. Nonetheless, it’s a far cry from when the US government tried designing an artificial reef off the Florida coast with more than two million discarded tyres, creating an environmental disaster in almost every imaginable way.
A tipping point
While these developments cannot cure us of the negative effects of our addiction to disposable items—that will require societal change, and a shift in corporate product and packaging design—innovations in the last decade are striking and merit cautious optimism.
A critical moment was the shift in Chinese policy. Before 2017, so much western trash was shipped abroad so cheaply that processing it was an afterthought. Sorting was often a highly manual process when it did occur. Now we are forced to face our waste and find cheaper, faster and more effective means to process it, a need heightened by an explosion of research demonstrating the pervasive health risks of leaving waste untreated.
That big change in what we do with trash has been followed by advancements in visual AI, sorting machinery and our understanding of the chemistry that makes up, and can break down, these materials. That has led to a surge in investment and potential in getting more out of what we throw away.
As taxes on non-recycled waste increase and more stringent targets are introduced by governments, the argument and, crucially, economics in favour of sorting and processing our garbage will further improve.
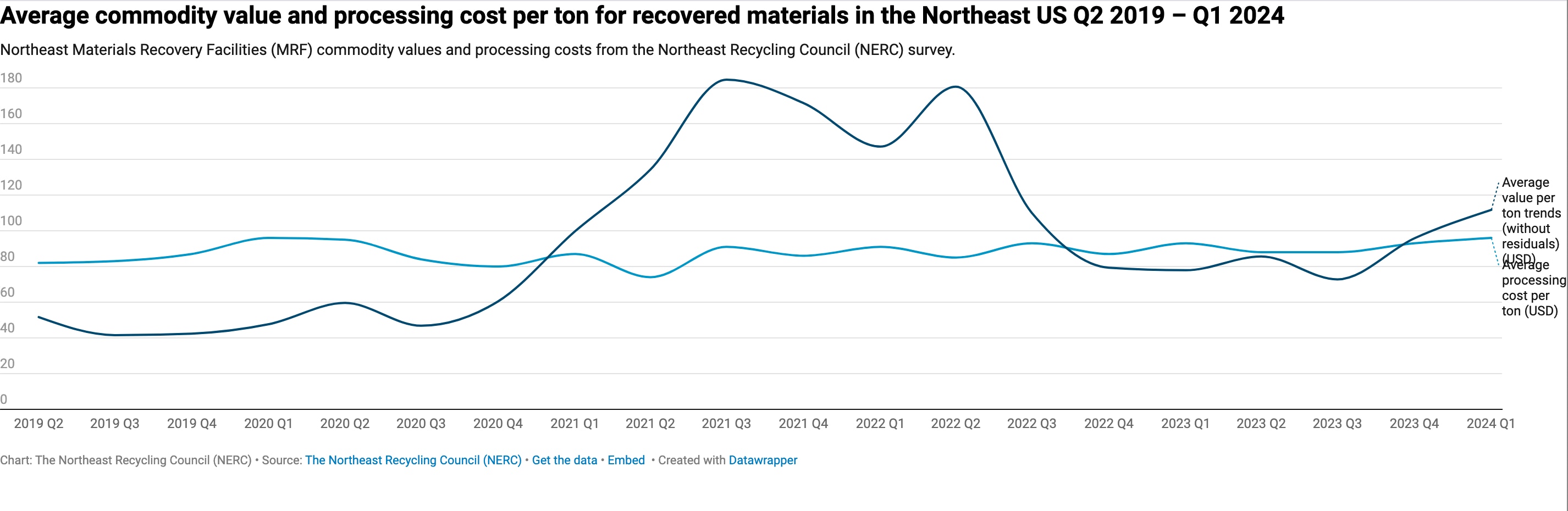
Over most of the post-China import ban period, the Northeast Recycling Council (NERC) surveyed recovery facilities in the Northeast US states. While the value per tonne of processed waste fluctuated heavily from 2019 to 2024, there are two key trends to consider from the data that illustrate incremental progress.
One is that the cost to process has remained the same throughout, which equates to a slight fall when adjusted for inflation. Secondly, the overall trendline has been for the value of sorted waste to go up to what appears to be an inflection point, where processed waste is consistently worth more than what it costs to process it.
As with climate change, we’re still not doing enough. But after years of literally burying the problem, we now have a positive direction to follow, underpinned by improving technology that, one day, could turn the tide on all this trash.
This article by guest writer Alex Hadwick is part of "Overlooked: Technologies quietly changing the world," a series of pieces that focus on advances making tangible everyday differences, but that also promise transformative change. Read the previous installments:
29 Nov 2024
-
Alex Hadwick
Illustration by Thomas Travert.
02/03
Related Insights
03/03
L’Atelier is a data intelligence company based in Paris.
We use advanced machine learning and generative AI to identify emerging technologies and analyse their impact on countries, companies, and capital.